Strainer Manufacturer
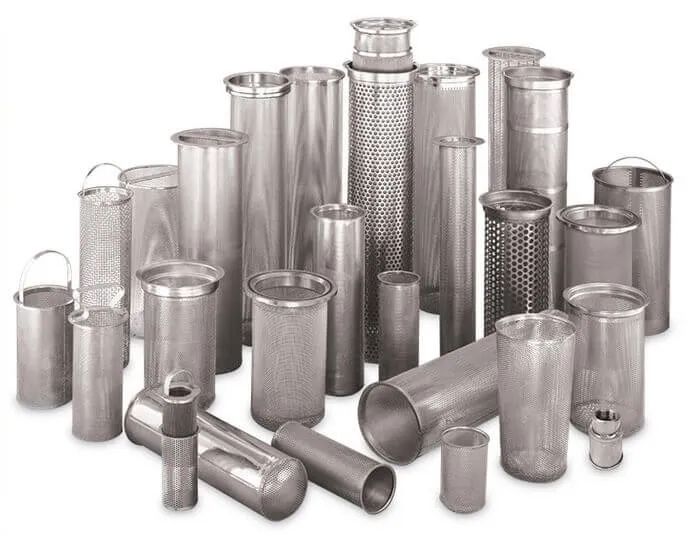
Strainer Manufacturer
JAE India stands out as a leading manufacturer of industrial strainers, catering to a diverse range of applications across numerous industries. Our commitment to quality, innovation, and exceptional customer service ensures we deliver the most effective filtration solutions for your specific needs.
Automatic Self-Cleaning Filters (ASCF)
Uninterrupted Filtration: ASCFs offer a significant advantage – continuous filtration with minimal downtime for cleaning. They utilize an automated backwashing mechanism that removes accumulated debris from the filter element without interrupting the flow of the process fluid. This is ideal for applications requiring uninterrupted filtration and where frequent manual cleaning is impractical.
Operating Principle: There are various ASCF designs, but a common principle involves a filtration element housed within a pressure vessel. The process fluid flows through the element, capturing unwanted particles on its surface. A differential pressure switch or timer triggers the backwashing cycle periodically. During backwashing, a cleaning fluid (often a portion of the filtered process fluid itself) is directed back through the element in the reverse direction, dislodging the accumulated particles. The flushed debris is then discharged from the system.
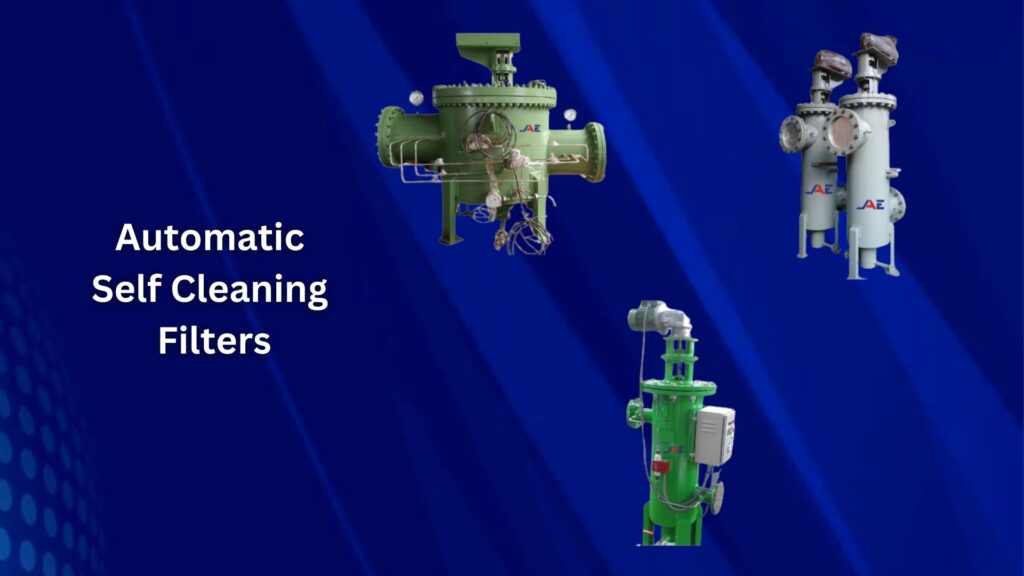
Technical Specifications
When selecting an ASCF, consider the following technical aspects:
Filtration Rating: This defines the minimum particle size the strainer can capture. JAE India offers ASCFs with various micron ratings to suit your specific application.
Differential Pressure Switch Settings: These settings determine when the backwashing cycle is initiated. A higher pressure differential indicates greater clogging and triggers backwashing to maintain optimal flow.
Cleaning Fluid Flow Rate & Duration: The flow rate and duration of the backwashing cycle are crucial for effective cleaning without excessive water usage. JAE India optimizes these parameters based on the specific filtration element and application.
Material of Construction: The ASCF housing, filtration element, and piping material selection depends on the process fluid compatibility, pressure rating, and temperature requirements. We offer options like stainless steel (304, 316L), carbon steel, or FRP (Fiberglass Reinforced Plastic) depending on the application.
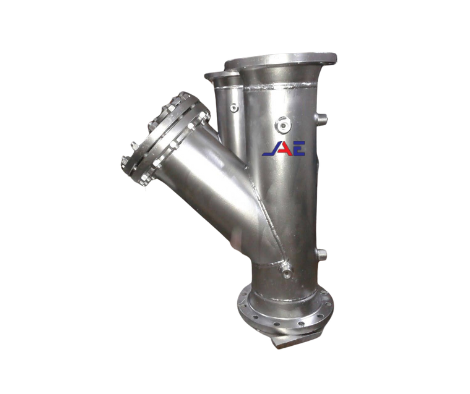
Y-Type Strainers
Compact & Cost-Effective: Y-type strainers are simple yet effective strainers known for their compact design and cost-effectiveness. They consist of a Y-shaped body with a removable basket element located at the bottom of the Y. The process fluid flows through the strainer body and changes direction at the Y-junction. Larger particles are captured in the basket element due to their inertia as the flow direction changes.
Basket Design & Material: Similar to basket type strainers, Y-type strainers utilize perforated metal baskets, wire mesh screens, or woven filter media depending on the desired filtration rating and particle size. The basket material is typically stainless steel for durability and corrosion resistance.
Cleaning Procedure: Y-type strainers require periodic manual cleaning. The process involves isolating the strainer from the pipeline, removing the cleanout plug at the bottom of the Y, and allowing the captured debris to drain out. Alternatively, the entire basket element can be removed for more thorough cleaning. JAE India offers Y-type strainers with user-friendly designs for easy removal of the cleanout plug or basket.
Technical Specifications: Key considerations for Y-type strainers include:
Mesh Size: This determines the minimum particle size captured by the strainer.
Strainer Size: The size of the Y-shaped body is selected based on the pipe diameter and desired flow rate. A larger strainer minimizes pressure drop across the strainer.
Pressure Rating: The strainer housing material and design must withstand the operating pressure within the pipeline. JAE India offers Y-type strainers for various pressure ratings.
Connection Options: Flanged, threaded, or socket-welded connections are available to suit your piping system requirements.
Basket Type Strainers
Simple & Efficient: Basket type strainers are widely used due to their simple design and ease of maintenance. They consist of a basket-shaped filter element housed within a pressure vessel. The process fluid flows through the basket, trapping particles larger than the basket’s mesh openings.
Basket Design & Material: The basket design can be perforated metal, a wire mesh screen, or a woven filter media depending on the desired filtration rating and particle size. The basket material is typically stainless steel for durability and corrosion resistance.
Cleaning Procedure: Basket type strainers require periodic manual cleaning. The process involves isolating the strainer from the pipeline, removing the basket, and cleaning it manually. JAE India offers user-friendly designs for easy basket removal and cleaning.
Technical Specifications: Key considerations for basket type strainers include:
Mesh Size: This determines the minimum particle size captured by the strainer.
Basket Capacity: The basket size needs to be sufficient to hold the anticipated amount of debris before requiring cleaning to avoid excessive pressure drop.
Pressure Rating: The strainer housing material and design must withstand the operating pressure within the pipeline. JAE India offers basket type strainers for various pressure ratings.
Connection Options: Flanged, threaded, or socket-welded connections are available to suit your piping system requirements.
Candle Filter Strainers
Pressure Vessel: The pressure vessel houses the candle elements and withstands the operating pressure of the process fluid. JAE India offers pressure vessels in various materials like stainless steel (304, 316L), carbon steel, or FRP (Fiberglass Reinforced Plastic) depending on the application’s pressure rating, temperature requirements, and compatibility with the process fluid.
Candle Elements: These are the heart of the candle filter strainer. They are typically hollow, cylindrical elements with a porous filtration media on the outer surface. The process fluid flows through the outer surface of the candles, and particles are captured on the filtration media. JAE India offers various candle media options to suit diverse needs:
Stainless Steel Mesh: Offers good durability and reusability, ideal for capturing larger particles.
Pleated Paper Elements: Provide high filtration efficiency for finer particles but may require periodic replacement.
Ceramic Elements: Offer excellent chemical resistance and high filtration efficiency, suitable for demanding applications.
Distribution Plate: This plate ensures even distribution of the process fluid across all the candle elements, maximizing filtration efficiency and minimizing pressure drop across the strainer.
Collection Chamber: The captured particles accumulate in the collection chamber at the bottom of the pressure vessel. This chamber is designed to facilitate easy removal of the debris during cleaning.
Cleaning Mechanism: Depending on the specific design, JAE India offers various cleaning mechanisms for candle filter strainers:
Backwashing: Similar to ASCFs, a backwashing cycle utilizes a cleaning fluid (often filtered process fluid) to dislodge accumulated particles from the candle media. This is suitable for continuous processes where downtime for cleaning needs to be minimized.
Manual Cleaning: Some candle filter designs require manual cleaning. The candles are removed from the pressure vessel, and the filtration media is cleaned manually. This is typically used for applications with lower flow rates or less critical processes where periodic shutdowns are acceptable.